Whether you’re in steel, glass production, oil and gas or another industry, chances are you’re using a recuperator to recover heat from flue gases. It’s arguably one of the most efficient ways to repurpose waste heat to preheat air entering the combustion system, significantly reducing fuel costs.
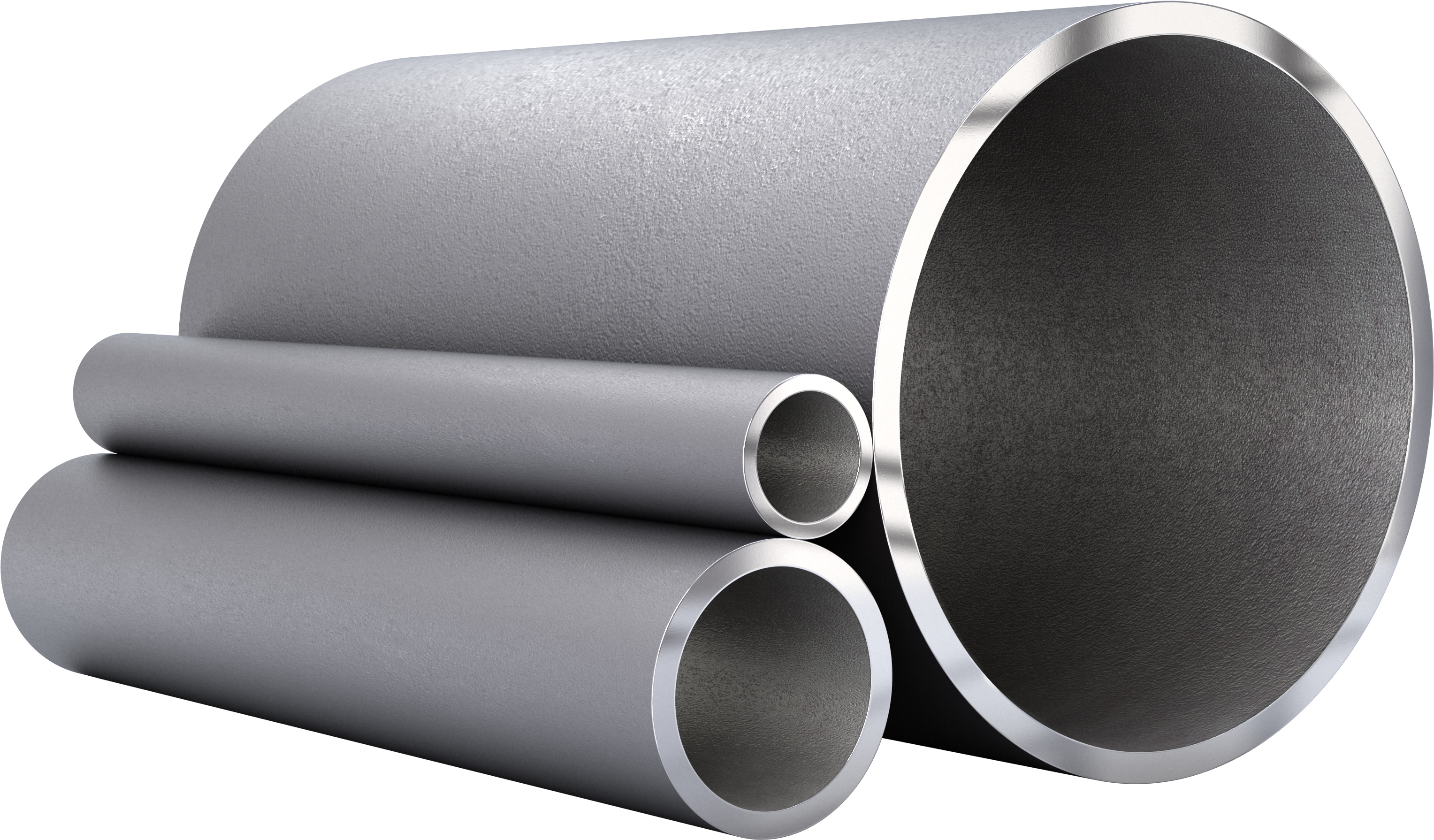
Counter-flow energy recovery
Also known as “counter-flow energy recovery heat exchangers,” these industrial units demand tubing that is both durable and highly corrosion resistant due, given the extreme temperatures they must endure. As critical components in the heat transfer process, these tubes play a vital role in substantially reducing fuel consumption and lowering operational costs.
The exact design and applications within the waste-heat process can vary quite a lot, but the primary uses are as follows:
Why Alleima customers use recuperators
- Waste heat recovery: Capture and repurpose heat that would otherwise be lost, improving overall system efficiency.
- Preheating combustion air: Transfer recovered heat to incoming air for combustion, increasing furnace or process efficiency.
- Reducing emissions: Lower fuel usage, thereby decreasing CO₂ and other emissions.
- Thermal regulation: Maintain consistent process temperatures, which improves product quality and energy utilization.
- Cost efficiency: Enable energy savings by reducing the need for external heat sources.
With a steelmaking legacy dating back to Sandviken, Sweden in 1862, we’ve teamed up with some of the most demanding industries all over the world. For recuperator tubing, the main industries we serve are as follows:
Common industries Alleima serves
- Steel and metal processing: Preheating air in furnaces and heat treatment lines.
- Glass production: Reusing heat from glass melting furnaces to heat combustion air.
- Carbon black production: Recycling heat from reactors for process efficiency.
- Petrochemical and chemical industries: Heat exchange in high-temperature reactors.
- Power generation: Improving energy recovery in combined heat and power (CHP) systems.
Fully integrated manufacturing
Alleima offers a broad range of stainless and high-alloy tubes, specifically designed for recuperators, produced in fully integrated and sustainable production processs. From melt to final tube, we maintain tight control over the tubing, conducting extensive destructive and nondestructive testing to ensure the highest quality. Our recuperator tubes are made of 80% recycled material and produced using fossil-free energy.
Delivering the highest quality
Thanks to the high-quality manufacturing process above, our recuperator tube offers excellent performance on key properties, such as
- Resistance to high-temperature oxidation at elevated temperatures
- Strong corrosion resistance to sulfurizing, carburizing and nitriding
- High mechanical strength to minimize stress and creep
- Erosion of tube surfaces is kept to a minimum
Below you can see our wide range of high-temperature corrosion resistant materials suitable for flue gas temperatures up to 1300ºC (2370ºF).
Materials for increased heat efficiency
The Alleima portfolio includes several materials allowing for higher operating temperature, enabling increased heat recovery and higher efficiency. Examples are Kanthal APMT and Alleima® 253 MA*.
Savings in fuel consumption at different waste gas and air preheat temperatures
Recuperator tube materials (other grades can be offered on request)
Alleima grade (UNS) | Description |
---|---|
Alleima® 253 MA* (UNS S30815) |
Austenitic stainless steel alloyed with nitrogen and REM (rare earth metals). Suitable for most types of conditions. |
Alleima® 353 MA* (UNS S35315) |
Austenitic stainless steel alloyed with nitrogen and REM (rare earth metals). Suitable for oxidizing, carburizing and nitriding conditions. |
Alleima® 4C54 (UNS S44600) |
Ferritic stainless steel with a high chromium content (26.5%) suitable for sulphudizing conditions. |
Sanicro® 31HT (UNS N08811/N08810) |
Austenitic stainless steel with good resistance to oxidation. Suitable for oxidizing, nitriding and carburizing conditions. |
Kanthal APM & Kanthal APMT |
Ferritic iron-chromium-aluminium (FeCrAl) stainless steel with superior oxidation properties. Suitable for sulphudizing conditions in the highest temperatures. |
*253 MA and 353 MA are trademarks owned by Outokumpu OY